
NM Tech CAN Projects
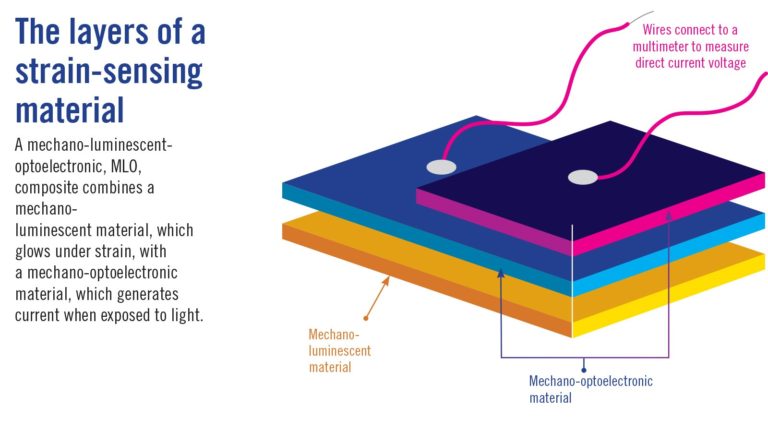
Autonomous Structural Composites for Next Generation Unmanned Aircraft Systems
Principal Investigator: Donghyeon Ryu, Assistant Professor, Dept. of Mechanical Engineering, NMIM&T
In this proposed study, PIs will devise autonomous structural composites capable of self-powered delamination detection in FRP composites and harvesting energy. The autonomous composites will be fabricated by embedding multifunctional thin films into structural FRP composites. The multifunctional thin films will be designed to perform self-powered strain sensing as well as energy conversion of ambient vibration to electrical energy. Research objective is three-fold. First, the copper-doped zinc sulfide (ZnS:Cu)/poly(3-hexylthionphene) (P3HT)-based multilayered thin films will be designed and optimized through theoretical and experimental studies. ML light emission of the ZnS:Cu-based layer and the photoactive P3HT-based layer will judiciously designed to exhibit multifunctional capability. The material and geometric design of the multilayered thin films will be optimized through in-depth studies for enhancing sensing capability, energy conversion efficiency, and micro-/nano-mechanical performance. Second, autonomous structural composites will be fabricated by embedding the designed ZnS:Cu/P3HT-based thin films into FRP composites. Multifunctional capabilities (i.e., self-powered delamination detection and energy harvesting) of the autonomous structural composites
will be validated under space environmental effects (e.g., thermal gradients, space radiations, and blast, among some others). Last, Aerostructures Test Wing (ATW) will be fabricated using the developed autonomous structural composites to be tested at Flight Loads Lab (FLL) at NASA Armstrong Flight Research Center (AFRC) using Ground Vibration Test (GVT) setup. The autonomous delamination detection capability of the autonomous ATW will be validated through vibration-based SHM framework (e.g., natural frequency shift and mode shape changes) in mid-range vibrational loadings. Furthermore, energy harvesting capability of the autonomous ATW will be validated under ambient vibrations. Space environmental effects will be studied on the performance of the autonomous ATW in the state-of-the-art facilities at FLL at NASA AFRC.
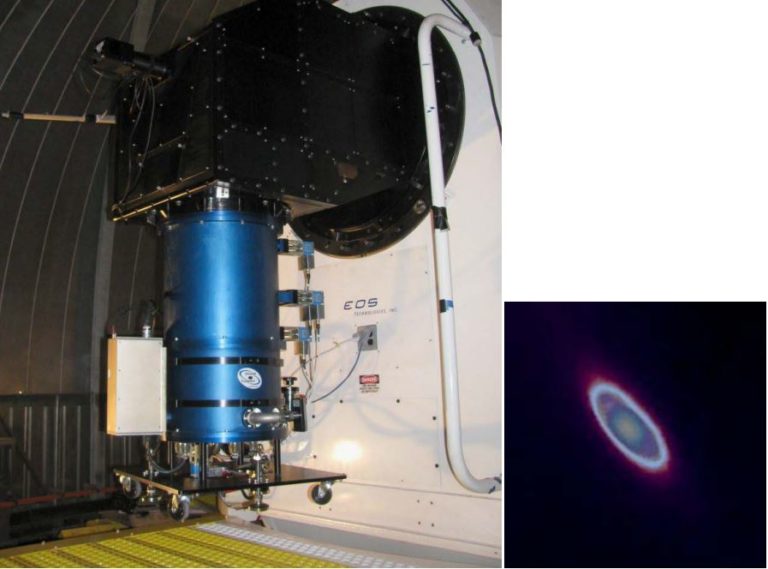
New Mexico Exoplanet Spectroscopic Survey Instrument (NESSI)
Co-Investigators: Michelle Creech-Eakman, Penelope Boston, David Westpfahl, Colby Jurgenson
To build a moderate resolution, highly-calibratible near-infrared exoplanet spectrometer, NESSI (New Mexico Tech Exoplanet Spectroscopic Survey Instrument), to study the atmospheric molecular signatures of transiting exoplanets; NESSI will be deployed as a facility instrument on the high-altitude Magdalena Ridge Observatory (MRO) 2.4-meter telescope. The need for NESSI relies on the fact that most astronomical infrared spectrometers are not sufficiently stable and repeatable (in terms of calibration, pointing, non-/correlated errors, etc.) to make repeated measurements at the 0.01% relative level from ground-based platforms. Our colleagues at JPL have recently developed a technique which can be used to mitigate nearly all of Earth’s atmospheric contributions, allowing a purpose-designed, dedicated survey instrument to overcome these failures.
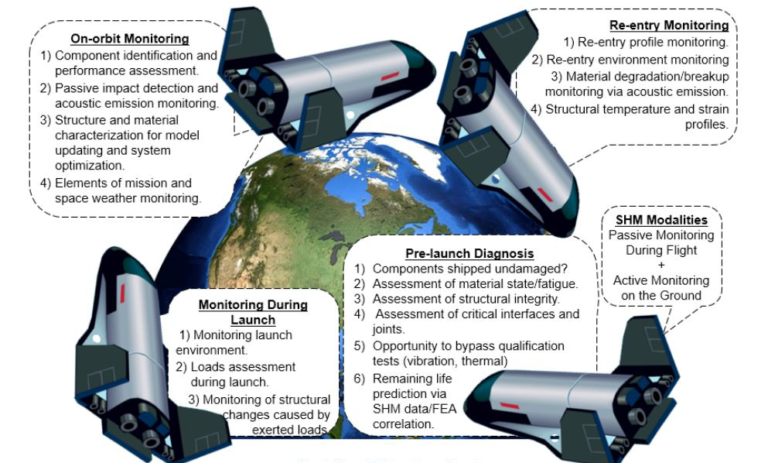
In Orbit Structural Health Monitoring of Space Vehicles
Principal Investigator: Andrei Zagrai, Professor and Department Chair, Mechanical Engineering, New Mexico Institute of Mining and Technology
A significant step in addressing the safety of space vehicles is development and testing of the flight information recorder, or “black box”. It is envisioned, that a structural health monitoring system (SHM) would be an integral part of the “black box” and would record information on structural integrity during all stages of spaceflight. In this project, the team proposes to investigate the effects of the space environment on piezoelectric sensors – active elements of SHM, to explore structural vibrations in microgravity and to demonstrate the feasibility of SHM during long term space missions. To achieve this goal, 1U and 3U payloads (depending on space available) are proposed that will fit into a Nanoracks system outside of the ISS. Mission duration is expected to be less than 1 year (1 year maximum) with minimum of crew time. The power requirement is estimated to approach a few watts. The data collected in the proposed experiment would also benefit the FAA Center for Commercial Space Transportation. The principal investigator is a mechanical engineering professor that has previously participated in a NASA EPSCoR project and launched several suborbital payloads through the NASA Flight Opportunity Program.